Welcome!
Team PTI has extensive experience with validation for medical devices. That's why we are able to identify...
12 things that will delay your molding validation.
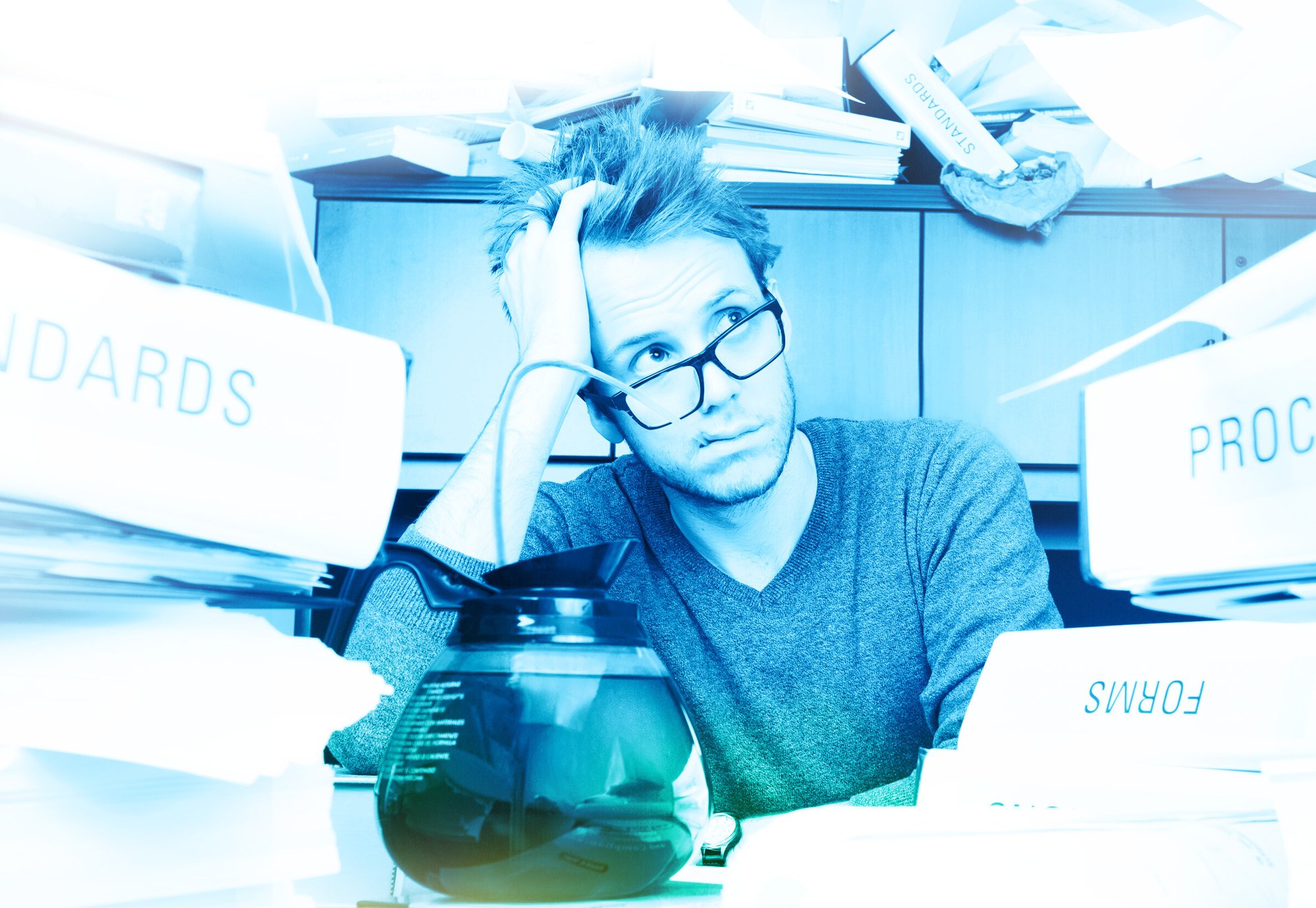
12 Things that Will Delay Your Molding Validation
1. Scope Changes
Define as much as possible up front.
What is required to qualify the part? 100% Layout, PPAP, or full IQ/OQ/PQ?
Consider documenting everything in the Master Validation Plan. Ensure at least 1 dimension critical to the process exists on the drawing. Make sure the deliverable is defined and understood by both teams.
2. Protocol / Report Review and Approvals
We recommend assigning dedicated personnel for customer approvals (no more than 2 MAX).
More people = More delays.
Utilize molders protocol / report templates. Ask for these documents up front.
3. Quality System Alignment
Rely on supplier qualification and standards in which molder is registered (ISO13485) / compliant to (CFR Part 820).
Utilize supplier quality system requirements to your advantage.
When system requirements do not align, delays will occur trying to determine what to do and the negotiations will add time to the front end of the project.
4. Excessive Critical Dimensions
3 Maximum for process validation / monitoring (this is all you need!) We recommend: Overall Length, Width, and Height.
Consider 20 critical dimensions on a 4-cavity tool = 14400 data points analyzed into 400 Cpk studies between OQ/PQ. Not to mention 20 Gage R&R studies. Three dimensions on 4-cavity tool = 2160 data points analyzed 72 Cpk studies.
Both paths lead to FDA CFR Part 820 and ISO 13485 compliance, chose wisely.
5. Critical Dimensions with GD&T Callouts
DO NOT DO THIS.
This will compound issues with timing as any fix or tweak to tooling will likely require the CMM to verify.
This is especially true for surface profiles. DO NOT rely on a surface profile as a process validation dimension!
6. Dimensions Out of Tolerance
Keep in mind that Every Out-of-Tolerance dimension will need to be addressed.
Steel change or drawing change. Who is the point person to make the decision? This is likely to happen on your validation so be prepared.
7. Dimensions not meeting Cpk Requirements or Normality
You'll need to make quick decision if this is OK “as is” or does it impact form/fit/function?
It's always best to help your molder understand how its impacting assembly to get best resolution possible. Keep in mind that the easiest path forward is always a drawing change if parts are functionally OK.
8. Excessively Tight Dimensional Tolerances
It's best to utilize SPI standards, which recommend tolerances based on the material type and the size of the feature.
Be rational. Remember a sheet of paper is .004”. Avoid tolerances less than +/-.002 and never specify tolerance less than +/-.001.
Plastic is forgiving and tolerances this tight drive cost and will likely delay your validation.
9. Bringing Part Dimensions into Spec by Pushing Process Limits
The result of this will be a smaller process window and other dimensions may be pushed out of spec.
95% of the time drawing updates are made to increase tolerance or shift nominal.
5% of the time we see issues with form/fit/function and a tooling change is required.
10. Cosmetic Standards not Achievable or Exceed Capabilities of Material or Molding Process
Again, utilize industry standards such as SPI “Cosmetic Specifications of Injection Molded Parts”.
- All exterior surfaces Class A
- Internal surfaces Class D
Avoid requirements like “no flash” or “no bubbles, scratches, etc.” as these become subjective (especially when parts are inspected with magnification).
11. Customer and Molder Inspection Data not Aligned
Stick to as many linear dimensions as possible!
There is rarely disagreement on these types of dimensions.
Avoid using different methods (i.e. CMM vs CT Scan).
12. CT Scan Required for Inspection
You should not rely on CT scanning for part verification during validation.
In addition to the high cost, your timing will likely be impacted sorting through and ‘scrubbing’ data.
CT scans can be helpful for troubleshooting (finding internal voids with non-transparent materials) but can also provide information overload.
More data, more problems!
Watch our Device Talks!
Simplify Injection Molding Validation to Boost Your Time to Market
Our Team PTI experts, Steve and Jon, talk with Tom from Device Talks Tuesdays about all things plastic part validation.
Learn valuable insights to reducing your validation time and getting to market quick.